3D printing provides various advantages that are dramatically changing the production scene. One significant advantage is quick prototyping. Traditional prototyping methods are time-consuming and expensive, necessitating the use of specialized tools and molds. Designers may use 3D printing to swiftly create and iterate prototypes, shortening the product development cycle and lowering time to market. Furthermore, customization and personalization are significant advantages of 3D printing. It enables widespread customisation, allowing producers to make unique, personalized items for specific clientele at no additional expense. This is especially useful in healthcare, where specialized medical implants and prosthesis can be personalized to a patient’s specific anatomy, and in the fashion and consumer goods industries, where it improves client happiness and brand loyalty.
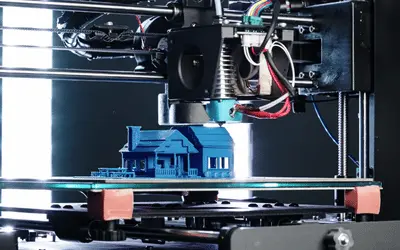
Furthermore, 3D printing excels at creating complex geometries with lightweight structures, which are typically difficult to produce using older methods. This capacity is critical in industries like aerospace and automotive, where lightweight and structurally optimized components may boost performance and fuel efficiency. The additive manufacturing process of 3D printing is also eco-friendly. By constructing objects layer by layer, it employs only the resources needed for the finished result, as opposed to subtractive procedures such as machining, which cause significant material waste. This reduction in waste improves sustainability and reduces resource expenditures.
Another big advantage of 3D printing is on-demand production, which allows businesses to produce products when they are needed rather than keeping vast stockpiles. This lowers storage costs and lessens the danger of overproduction, which is especially useful in businesses that require immediate availability of certain components, such as replacement parts and maintenance. Furthermore, 3D printing streamlines supply chains by allowing for the creation of parts and goods closer to the point of use, lowering transportation costs and the risks associated with global supply chain interruptions. Materials science innovations are expanding the possibilities of 3D printing, with new materials such as metals, ceramics, and composites being produced for additive manufacturing, allowing for fresh applications in domains ranging from medical devices to high-performance engineering.
The adaptability of 3D printing encourages innovation in product creation by allowing engineers and designers to experiment with new ideas, structures, and functionalities without the constraints of traditional manufacturing techniques. This fosters a culture of invention, resulting in new goods. In medicine, 3D printing enables breakthroughs in individualized therapy and bioprinting, with custom implants, prosthesis, and surgical equipment designed for particular patients. Bioprinting, or the production of tissue and organ structures, has the potential to transform organ transplantation and regenerative medicine. Furthermore, 3D printing is becoming an indispensable tool in education and training, allowing students and professionals to engage in hands-on learning, comprehend complex concepts, experiment with design and engineering principles, and develop practical skills that are increasingly important in the modern workforce. To summarize, 3D printing has immense and disruptive potential for the manufacturing business, ushering in a new era of creativity, efficiency, and sustainability.